Journal Description
Applied Mechanics
Applied Mechanics
is an international, peer-reviewed, open access journal on applied mechanics, published quarterly online by MDPI. The South African Association for Theoretical and Applied Mechanics (SAAM) is affiliated with Applied Mechanics and its members receive discounts on the article processing charges.
- Open Access— free for readers, with article processing charges (APC) paid by authors or their institutions.
- High Visibility: indexed within ESCI (Web of Science), Scopus and other databases.
- Rapid Publication: manuscripts are peer-reviewed and a first decision is provided to authors approximately 23.1 days after submission; acceptance to publication is undertaken in 4.9 days (median values for papers published in this journal in the second half of 2024).
- Journal Rank: CiteScore - Q2 (Engineering (miscellaneous))
- Recognition of Reviewers: APC discount vouchers, optional signed peer review, and reviewer names published annually in the journal.
Latest Articles
State-of-the-Art Navigation Systems and Sensors for Unmanned Underwater Vehicles (UUVs)
Appl. Mech. 2025, 6(1), 10; https://doi.org/10.3390/applmech6010010 - 2 Feb 2025
Abstract
Researchers are currently conducting several studies in the field of navigation systems and sensors. Even in the past, there was a lot of research regarding the field of velocity sensors for unmanned underwater vehicles (UUVs). UUVs have various services and significance in the
[...] Read more.
Researchers are currently conducting several studies in the field of navigation systems and sensors. Even in the past, there was a lot of research regarding the field of velocity sensors for unmanned underwater vehicles (UUVs). UUVs have various services and significance in the military, scientific research, and many commercial applications due to their autonomy mechanism. So, it’s very crucial for the proper maintenance of the navigation system. Reliable navigation of unmanned underwater vehicles depends on the quality of their state determination. There are so many navigation systems available, like position determination, depth information, etc. Among them, velocity determination is now one of the most important navigational criteria for UUVs. The key source of navigational aids for different deep-sea research projects is water currents. These days, many different sensors are available to monitor the UUV’s velocity. In recent times, there have been five primary types of sensors utilized for UUV velocity forecasts. These include Doppler Velocity Logger sensors, paddlewheel sensors, optical sensors, electromagnetic sensors, and ultrasonic sensors. The most popular sensing sensor for estimating velocity at the moment is the Doppler Velocity Logger (DVL) sensor. DVL sensor is the most fully developed sensor for UUVs in recent years. In this work, we offer an overview of the field of navigation systems and sensors (especially velocity) developed for UUVs with respect to their use with tidal current sensing in the UUV setting, including their history, evolution, current research initiatives, and anticipated future.
Full article
(This article belongs to the Special Issue Early Career Scientists’ (ECS) Contributions to Applied Mechanics (2nd Edition))
Open AccessReview
An Investigation of the Mechanical Properties of Concrete with Different Types of Waste Plastics for Rigid Pavements
by
Nuha S. Mashaan and Cherrie Ann E. Ouano
Appl. Mech. 2025, 6(1), 9; https://doi.org/10.3390/applmech6010009 - 31 Jan 2025
Abstract
The increasing demand for sustainable construction practices has prompted the exploration of innovative materials, such as waste plastics, to enhance both the environmental and mechanical performance of concrete, particularly for rigid pavements. This review investigates the mechanical properties of concrete incorporating four types
[...] Read more.
The increasing demand for sustainable construction practices has prompted the exploration of innovative materials, such as waste plastics, to enhance both the environmental and mechanical performance of concrete, particularly for rigid pavements. This review investigates the mechanical properties of concrete incorporating four types of waste plastics—high-density polyethylene (HDPE), low-density polyethylene (LDPE), polyvinyl chloride (PVC), and polypropylene (PP). The primary focus is on how these materials affect key mechanical properties, including compressive strength, tensile strength, and flexural strength. The analysis reveals that HDPE and PP, at optimal levels (5–10%), can enhance flexural and crack resistance, making them suitable for non-structural applications. Conversely, LDPE and PVC tend to reduce both compressive and tensile strengths at higher substitution levels due to poor bonding with cementitious materials. Despite these challenges, incorporating waste plastics into concrete presents significant environmental and economic benefits, including plastic waste reduction and lower reliance on natural aggregates. The review also highlights the need for further research on improving plastic–cement bonding through surface treatments and hybrid mix designs. This study contributes to the growing body of knowledge aimed at promoting the use of waste plastics in concrete, offering insights for the development of sustainable, high-performance construction materials.
Full article
Open AccessArticle
Force and Stress Simulation in Experimentable Digital Twins Using the Transfer Matrix Method
by
Sebastian Schmid, Dorit Kaufmann, Ulrich Dahmen, Finn Eggers, Ioannis Valais, Kai-Uwe Schröder and Jürgen Roßmann
Appl. Mech. 2025, 6(1), 8; https://doi.org/10.3390/applmech6010008 - 31 Jan 2025
Abstract
Experimentable Digital Twins are capable of combining different simulation domains on a system level. This has been shown for a multitude of simulation domains, e.g., rigid body dynamics, control, sensors, kinematics, etc., and application scenarios, e.g., automotive, space, and industrial engineering. In our
[...] Read more.
Experimentable Digital Twins are capable of combining different simulation domains on a system level. This has been shown for a multitude of simulation domains, e.g., rigid body dynamics, control, sensors, kinematics, etc., and application scenarios, e.g., automotive, space, and industrial engineering. In our work, we investigate how to include structural loads into an Experimentable Digital Twin while maintaining computational efficiency and interoperability on a system level. We combine rigid body dynamics with the transfer matrix method to simulate forces and stresses. We show our approach for statically determinate beam structures in a simulation on a system level and validate it experimentally and numerically with static and dynamic example problems. The results show a strong agreement in these comparisons, confirming the accuracy and reliability of our method. For practical applications, we see force and stress simulation using the transfer matrix method as an additional tool to facilitate simulation-based engineering in the early stages of structural design processes, e.g., when dealing with uncertain loading conditions and operational complexity on a system level.
Full article
Open AccessArticle
Design Considerations for a Compressed Stiffened Plate with Skin–Stringer Debonding Based on the Evaluation of Adhesive Layer Stress Distribution
by
Giacomo Frulla and Giovanni Parente
Appl. Mech. 2025, 6(1), 7; https://doi.org/10.3390/applmech6010007 - 30 Jan 2025
Abstract
An extensive application of stiffened panels is considered standard for aerospace wing construction both for reducing the structural weight and fulfilling the regulatory requirements. The connection based on the adhesive layer between the skin and stringer introduces the possibility of debonding during operative
[...] Read more.
An extensive application of stiffened panels is considered standard for aerospace wing construction both for reducing the structural weight and fulfilling the regulatory requirements. The connection based on the adhesive layer between the skin and stringer introduces the possibility of debonding during operative conditions. The design procedure is strongly influenced by this anomaly, requiring the definition of a criterion for identifying the limit in debonding extension for safe operation. A procedure based on the investigation of the stress state in the adhesive layer is proposed in order to identify the typical behaviour of compressed plate, including damage situation, and a specific indication for design procedure is derived based on the debonding dimension. Critical and post-critical configuration were investigated both globally and locally to fix sensitive parameters. A conclusive guideline is discussed and presented. The analysis is applied to an isotropic plate in order to point out the main characteristics of the related design procedure. No conceptual changes are expected with the introduction of composite material that can influence the distribution of stress according to the chosen lay-up but not the basic design concept in the plate behaviour.
Full article
(This article belongs to the Special Issue Mechanical Design Technologies for Beam, Plate and Shell Structures (3rd Edition))
►▼
Show Figures
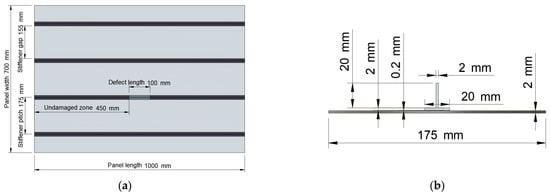
Figure 1
Open AccessArticle
Oxyacetylene Flame Forming of Thick Steel Plates
by
Jalal Joudaki, Mehdi Safari and Fábio A. O. Fernandes
Appl. Mech. 2025, 6(1), 6; https://doi.org/10.3390/applmech6010006 - 21 Jan 2025
Abstract
One of the most widely used processes in ship hull plate manufacturing is the flame forming process (FFP). In this work, the fabrication of saddle-shaped specimens with FFP using a spiral irradiating pattern is studied experimentally. The deformation of the deformed plates by
[...] Read more.
One of the most widely used processes in ship hull plate manufacturing is the flame forming process (FFP). In this work, the fabrication of saddle-shaped specimens with FFP using a spiral irradiating pattern is studied experimentally. The deformation of the deformed plates by FFP based on the spiral irradiating pattern is affected by process parameters such as the pitch of spiral passes (PSP), the radius of the starting circle (RSC), and the number of irradiation passes (NIP). However, in this work, the effects of process parameters on the deformation of SSS are statistically examined by the design of experiment (DOE) method based on response surface methodology (RSM). The experimental and statistical results show that the deformation of flame-formed SSS increases with the increase in RSC and NIP and the decrease in PSP. In addition, the results of the optimization procedure demonstrate that the maximum value of deformations of flame-formed saddle-shaped specimens is achieved by adjusting the process parameters as follows: PSP = 10 mm, RSC = 75 mm, and five NIPs.
Full article
(This article belongs to the Special Issue Thermal Mechanisms in Solids and Interfaces)
►▼
Show Figures
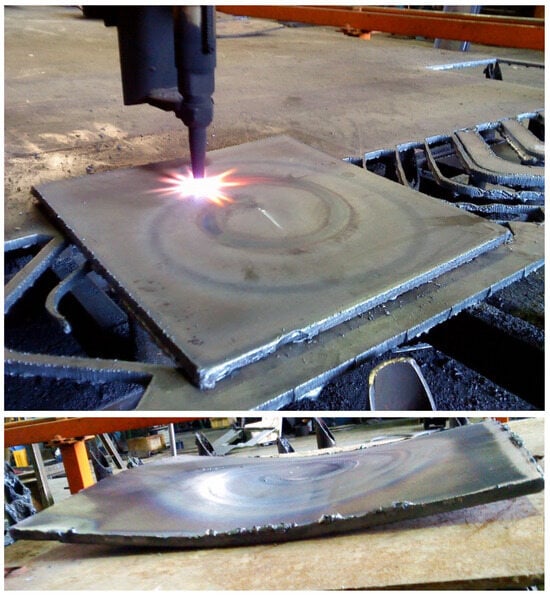
Figure 1
Open AccessArticle
Analysis of the Surface Quality Characteristics in Hard Turning Under a Minimal Cutting Fluid Environment
by
Sandip Mane, Rajkumar Bhimgonda Patil, Anindita Roy, Pritesh Shah and Ravi Sekhar
Appl. Mech. 2025, 6(1), 5; https://doi.org/10.3390/applmech6010005 - 17 Jan 2025
Abstract
►▼
Show Figures
This paper analyzes the surface quality characteristics, such as arithmetic average roughness (Ra), maximum peak-to-valley height (Rt), and average peak-to-valley height (Rz), in hard turning of AISI 52100 steel using a (TiN/TiCN/Al2O3) coated carbide insert under a minimal cutting
[...] Read more.
This paper analyzes the surface quality characteristics, such as arithmetic average roughness (Ra), maximum peak-to-valley height (Rt), and average peak-to-valley height (Rz), in hard turning of AISI 52100 steel using a (TiN/TiCN/Al2O3) coated carbide insert under a minimal cutting fluid environment (MCFA). MCFA, a sustainable high-velocity pulsed jet technique, reduces harmful effects on human health and the environment while improving machining performance. Taguchi’s L27 orthogonal array was used to conduct the experiments. The findings showed that surface roughness increases with feed rate, identified as the most influential parameter, while the depth of cut shows a negligible effect. The main effects plot of signal-to-noise (S/N) ratios for the combined response of Ra, Rt, and Rz revealed the optimal cutting conditions: cutting speed of 140 m/min, feed rate of 0.05 mm/rev, and depth of cut of 0.3 mm. Feed rate ranked highest in influence, followed by cutting speed and depth of cut. The lower values of surface roughness parameters were observed in the ranges of Ra ≈ 0.248–0.309 µm, Rt ≈ 2.013–2.186 µm, and Rz ≈ 1.566 µm at a feed rate of 0.05–0.07 mm/rev. MCFA-assisted hard turning reduces surface roughness by 35–40% compared to dry hard turning and 10% to 24% when compared to the MQL technique. Moreover, this study emphasizes the significant environmental benefits of MCFA, as it incorporates minimal eco-friendly cutting fluids that minimize ecological impact while enhancing surface finish.
Full article

Figure 1
Open AccessArticle
Behavior of Micropile (Type D) Subjected to Vertical Load: Parametric Numerical Studies
by
Mo’men Ayasrah
Appl. Mech. 2025, 6(1), 4; https://doi.org/10.3390/applmech6010004 - 14 Jan 2025
Abstract
►▼
Show Figures
Micropiles, small-diameter-drilled and grouted piles, are often used to provide foundation support in challenging ground conditions. This research seeks to understand the behavior of Type D micropiles (pressure-grouted) within layered soil profiles. Layered soils frequently create complexity because of differences in stiffness, strength,
[...] Read more.
Micropiles, small-diameter-drilled and grouted piles, are often used to provide foundation support in challenging ground conditions. This research seeks to understand the behavior of Type D micropiles (pressure-grouted) within layered soil profiles. Layered soils frequently create complexity because of differences in stiffness, strength, and permeability, which impact load transfer and the interaction between the micropiles and the surrounding soil. Type D micropiles use pressure injection, which results in enhanced skin friction, better grout–soil contact, and a greater capacity to carry loads. A set of numerical simulations was conducted to analyze the behavior of the micropile Type D under axial loading, which was evaluated by considering factors such as micropile diameter, spacing, and inclination. The results indicated that increasing the diameter of a micropile significantly improves its performance by enhancing load transfer and structural stiffness, as well as reducing soil deformation and settlement. In addition, for vertical micropiles and those with inclination angles of 10° and 20°, stiffness increased with diameter, while axial displacement remained constant at a 45° inclination. Furthermore, larger diameters reduced lateral displacements up to 20° inclination angles by increasing stiffness, but lateral deflection increased at 45° due to greater lateral load components. The bending moment increased with inclination angle, driven by higher horizontal loads and increased eccentricity, while spacing had little effect for angles greater than 20° due to effective load redistribution.
Full article
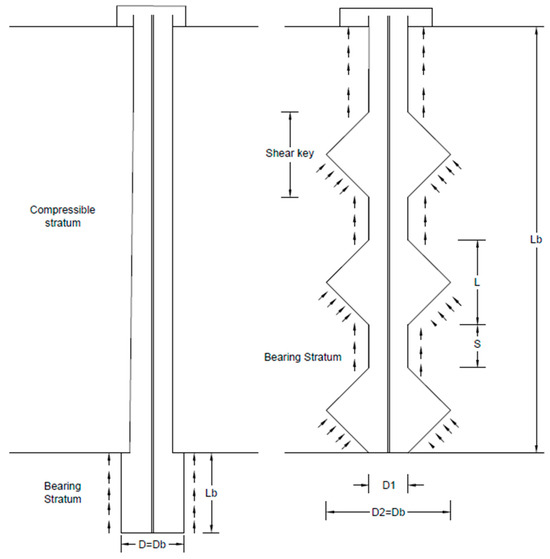
Figure 1
Open AccessArticle
Performance of Microconcretes with Different Percentages of Recycled Tire Rubber Granulate
by
Purificación Bautiste Villanueva, María Isabel Prieto Barrio and Alfonso Cobo Escamilla
Appl. Mech. 2025, 6(1), 3; https://doi.org/10.3390/applmech6010003 - 7 Jan 2025
Abstract
►▼
Show Figures
This paper investigates the short-term behavior of microconcretes with recycled rubber (RmCs) for extensive use as structural and non-structural materials. The physical and mechanical properties of a typical microconcrete composition have been experimentally evaluated by replacing the fine aggregate with rubber granules in
[...] Read more.
This paper investigates the short-term behavior of microconcretes with recycled rubber (RmCs) for extensive use as structural and non-structural materials. The physical and mechanical properties of a typical microconcrete composition have been experimentally evaluated by replacing the fine aggregate with rubber granules in volumetric percentages of 10%, 20%, and 30%. The results obtained are compared with the data provided by other authors for crumb rubber concretes (CRCs). Material investment costs have also been estimated to determine the economic impact of using rubber as a fine aggregate in these products. It is observed that the use of small percentages of recycled rubber (up to 20%) produces significant increases in slump as well as important drops in compressive strength, although it substantially improves its post-critical behavior. These trends tend to stabilize with higher percentages of rubber (30%). It is also noted that the experimental results and predictive models developed for concretes are not applicable to microconcretes, so more specific research is desirable for this type of product. Regarding the economic profitability of the investment in RmCs, it is found that it is necessary to make recycled rubber cheaper and to ensure its technological performance in order to guarantee the quality of the final product.
Full article
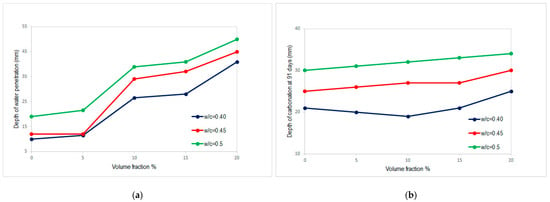
Figure 1
Open AccessArticle
A Novel 3D Reinforced Particle Model for Reinforced Concrete Fracture Assessment: Formulation and Validation
by
Nuno Monteiro Azevedo, Maria Luísa Braga Farinha and Sérgio Oliveira
Appl. Mech. 2025, 6(1), 2; https://doi.org/10.3390/applmech6010002 - 5 Jan 2025
Abstract
►▼
Show Figures
Rigid particle models (PMs) that explicitly consider the influence of the aggregate structure and its physical interaction mechanisms have been used to predict cracking phenomena in concrete. PMs have also been applied to reinforced concrete fracture, but the known studies have adopted simplified
[...] Read more.
Rigid particle models (PMs) that explicitly consider the influence of the aggregate structure and its physical interaction mechanisms have been used to predict cracking phenomena in concrete. PMs have also been applied to reinforced concrete fracture, but the known studies have adopted simplified reinforcement and reinforcement/particle interaction models. In this work, a novel 3D explicit discrete element formulation of reinforcement bars discretized through several rigid cylindrical segments is proposed, allowing the 3D reinforced particle model (3D-RPM) to be applied to reinforced concrete fracture studies, namely for shear failure. The 3D-RPM is evaluated using known three-point and four-point bending tests on reinforced concrete beams without stirrups and on known shear transfer tests due to dowel action. The 3D-RPM model is shown to reproduce the crack propagation, and the load displacement response observed experimentally for different steel contents under three-point bending, for different beam sizes, under four-point bending, and for different bar diameters, under shear. The validation examples highlight the importance of including a nonlinear reinforcement/particle interaction model. As shown, an elastic model contact leads to higher vertical loads in three-point and four-point bending tests for the same set of contact properties and, in the shear tests, leads to an overestimation of the maximum shear strength and to an increase in the model initial stiffness.
Full article
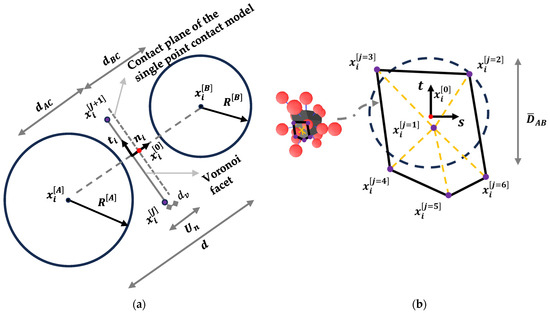
Figure 1
Open AccessArticle
Numerical Model for Studying the Properties of a New Friction Damper Developed Based on the Shell with a Helical Cut
by
Andrii Velychkovych, Vasyl Mykhailiuk and Andriy Andrusyak
Appl. Mech. 2025, 6(1), 1; https://doi.org/10.3390/applmech6010001 - 2 Jan 2025
Abstract
Friction dampers based on the effects of dry friction are attractive to engineers because of their simple design, low manufacturing and maintenance costs, and high efficiency under heavy loads. This study proposes a new damper design based on an open shell with a
[...] Read more.
Friction dampers based on the effects of dry friction are attractive to engineers because of their simple design, low manufacturing and maintenance costs, and high efficiency under heavy loads. This study proposes a new damper design based on an open shell with a deformable filler, with the shell cut along a cylindrical helical line. The key idea in developing the design was to use the bending effect of the shell in contact with the weakly compressible filler. Another idea was to use the frictional interaction between the filler and the open shell to obtain the required damping characteristics. The working hypothesis of this study was that, ceteris paribus, a change in the configuration of the shell cut would cause a change in the stiffness of the structure. To analyse the performance characteristics of the proposed damper and test the hypothesis put forward, a numerical model of the shell damper was built, and a boundary value problem was formulated and solved for the frictional interaction between the shell cut along the helical line and the weakly compressible filler, taking into account the dry friction forces between them. As a result, the strength, stiffness, and damping properties of the developed damper were investigated, and a comparative analysis of the new design with the prototype was carried out. It is predicted that the proposed friction damper will be used in the energy and construction industries, in particular in drilling shock absorbers for the oil and geothermal industries, as well as in earthquake-resistant structures.
Full article
(This article belongs to the Special Issue Mechanical Design Technologies for Beam, Plate and Shell Structures (3rd Edition))
►▼
Show Figures
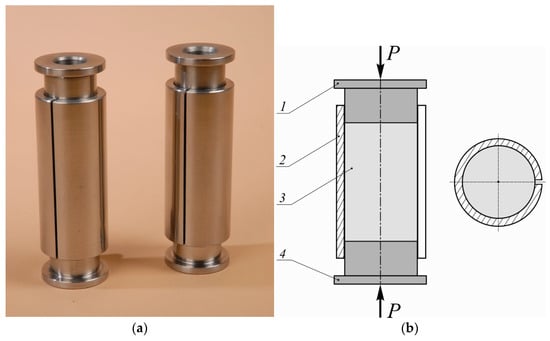
Figure 1
Open AccessArticle
A Newly Developed Compressed Air Cannon Test Bench Designed for Multi-Impact Analysis of Composite Structures
by
Ayoub Soufri, Ameur Chettah, Benoît Piezel and Christophe Bouvet
Appl. Mech. 2024, 5(4), 997-1010; https://doi.org/10.3390/applmech5040055 - 16 Dec 2024
Abstract
Understanding the response and damage evolution of structures subjected to multiple impact events is essential for designing resilient structures capable of withstanding complex loading scenarios, such as impacts from hail, gravel or foreign object debris. This article presents the development and characterization of
[...] Read more.
Understanding the response and damage evolution of structures subjected to multiple impact events is essential for designing resilient structures capable of withstanding complex loading scenarios, such as impacts from hail, gravel or foreign object debris. This article presents the development and characterization of a novel test bench, the “Compressed air multi-cannon”, designed specifically for studying the multi-impact behavior of composite materials. This test bench offers advantages over traditional impact testing methods by enabling controlled and adjustable impact parameters, including number of impacts, spatial and temporal lag, energy, angle and impactor dimensions. The primary objective of this work is to provide a detailed description of the test bench design, construction, and validation procedures. Key components such as the pressurized air system, projectile launch mechanism, target mounting arrangement, and data acquisition system are discussed. Experimental methodologies for assessing multi-impact response, specimen preparation, instrumentation, and data analysis techniques are outlined. Through a series of single-impact and multi-impact tests, distinctive damage mechanisms and energy absorption characteristics were observed in composite structures, revealing significant differences in how composites respond under single- and multi-impact conditions. It was found that the single-impact configuration remains particularly critical compared to multi-impact configurations with a high number of impacts. However, further testing is required to determine whether this result holds true under varying impact parameters, highlighting the unique value of this machine for exploring new, realistic questions in the literature.
Full article
(This article belongs to the Special Issue Early Career Scientists’ (ECS) Contributions to Applied Mechanics (2nd Edition))
►▼
Show Figures
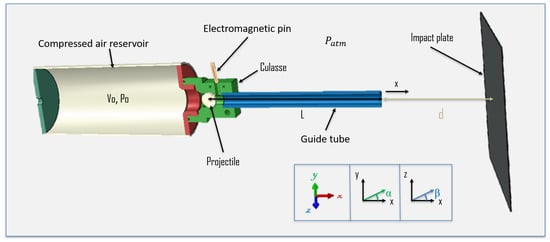
Figure 1
Open AccessArticle
Transversal Vortex-Induced Vibration of a Circular Cylinder in Tandem with a Stationary Square Structure
by
Henry Francis Annapeh and Victoria Kurushina
Appl. Mech. 2024, 5(4), 978-996; https://doi.org/10.3390/applmech5040054 - 12 Dec 2024
Abstract
This paper considers a system with two offshore structures in tandem, where the upstream square structure is fixed and the downstream circular structure has one degree of freedom. Cylinders are subject to uniform and linearly sheared flow conditions. The dynamics of the downstream
[...] Read more.
This paper considers a system with two offshore structures in tandem, where the upstream square structure is fixed and the downstream circular structure has one degree of freedom. Cylinders are subject to uniform and linearly sheared flow conditions. The dynamics of the downstream structure are investigated by using a computational fluid dynamics approach for a Reynolds number range of 1000–6500 at the centerline. The spacing ratio for the tandem structures is L/D = 6 in this work, corresponding to the wake interference regime. The effect of the shear parameter on the development of vortex-induced vibrations in the lock-in state within the downstream structure is studied, in comparison with the lock-in of an isolated circular structure. The results of this research include statistics on the displacement amplitude, drag and lift coefficients, frequency ratio, time histories and contours of vorticity. The results obtained show the maximum displacement amplitude of the isolated structure in a uniform flow at the level of 0.8 diameters during the upper branch. The investigation also shows a later development in the maximum displacement during the upper branch of the downstream structure under shear flow conditions, with the highest maximum displacement of 1.18 diameters seen for the shear parameter of 0.05.
Full article
(This article belongs to the Special Issue Early Career Scientists’ (ECS) Contributions to Applied Mechanics (2nd Edition))
►▼
Show Figures
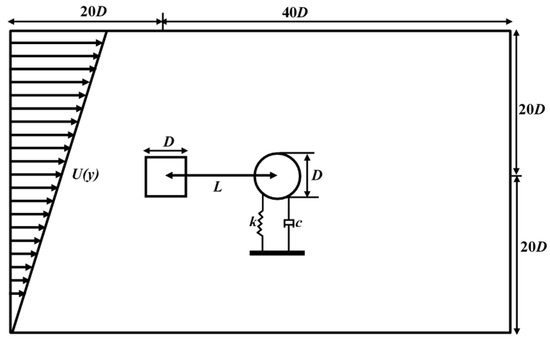
Figure 1
Open AccessArticle
Fluid Interaction Analysis for Rotor-Stator Contact in Response to Fluid Motion and Viscosity Effect
by
Desejo Filipeson Sozinando, Bernard Xavier Tchomeni and Alfayo Anyika Alugongo
Appl. Mech. 2024, 5(4), 964-977; https://doi.org/10.3390/applmech5040053 - 8 Dec 2024
Abstract
►▼
Show Figures
Fluid–structure interaction introduces critical failure modes due to varying stiffness and changing contact states in rotor-stator systems. This is further aggravated by stress fluctuations due to shaft impact with a fixed stator when the shaft rotates. In this paper, the investigation of imbalance
[...] Read more.
Fluid–structure interaction introduces critical failure modes due to varying stiffness and changing contact states in rotor-stator systems. This is further aggravated by stress fluctuations due to shaft impact with a fixed stator when the shaft rotates. In this paper, the investigation of imbalance and rotor-stator contact on a rotating shaft was carried out in viscous fluid. The shaft was modelled as a vertical elastic rotor system based on a vertically oriented elastic rotor operating in an incompressible medium. Implicit representation of the rotating system including the rotor-stator contact and the hydrodynamic resistance was formulated for the coupled system using the energy principle and the Navier–Stokes equations. Additionally, the monolithic approach included an implicit strategy of the rotor-stator fluid interaction interface conditions in the solution methodology. Advanced time-frequency methods, such as Hilbert transform, continuous wavelet transform, and estimated instantaneous frequency maps, were applied to extract the vibration features of the dynamic response of the faulted rotor. Time-varying stiffness due to friction is thought to be the main reason for the frequency fluctuation, as indicated by historical records of the vibration displacement, whirling orbit patterns of the centre shaft, and the amplitude–frequency curve. It has also been demonstrated that the augmented mass associated with the rotor and stator decreases the natural frequencies, while the amplitude signal remains relatively constant. This behaviour indicates a quasi-steady-state oscillatory condition, which minimises the energy fluctuations caused by viscous effects.
Full article
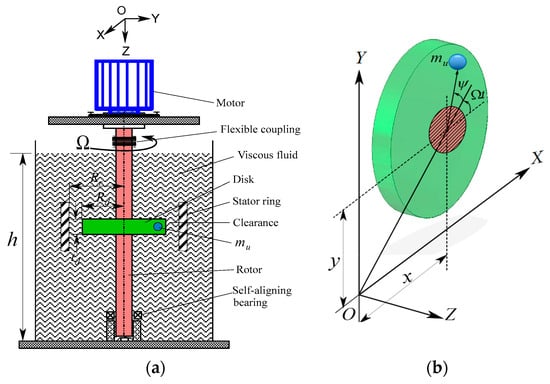
Figure 1
Open AccessArticle
Seismic and Post-Seismic Ductility and Forces of Mid-Story Pin Moment-Resisting Frames Based on Scale of Local Deformation of I-Beam’s Segments
by
Atsushi Suzuki, Ruiyu Che and Yoshihiro Kimura
Appl. Mech. 2024, 5(4), 938-963; https://doi.org/10.3390/applmech5040052 - 4 Dec 2024
Abstract
A mid-story pin system to avoid moment-resisting frame column failure during seismic action was proposed recently. The solution consists of a reinforced concrete (RC) pier protruding from the foundations, the steel column connected with the superstructure, and plates and the anchor bolt working
[...] Read more.
A mid-story pin system to avoid moment-resisting frame column failure during seismic action was proposed recently. The solution consists of a reinforced concrete (RC) pier protruding from the foundations, the steel column connected with the superstructure, and plates and the anchor bolt working as a pinned connection in between. This paper utilizes shell finite element analysis (FEA) models to examine the demanded column-to-beam strength ratio to keep the column elastic and maximize the story drift at the moment of beam buckling of the frame. The method of calculating post-seismic residual strength based on maximal buckling deformation of the beam is also proposed.
Full article
(This article belongs to the Special Issue Mechanical Design Technologies for Beam, Plate and Shell Structures (3rd Edition))
►▼
Show Figures
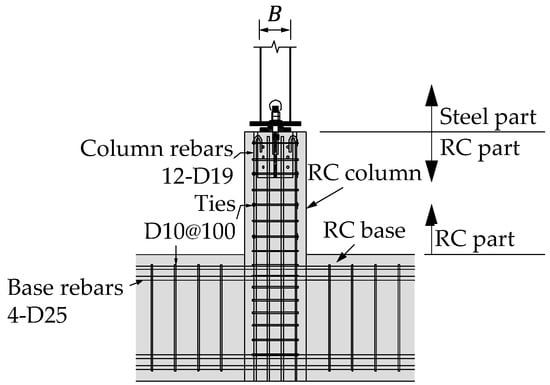
Figure 1
Open AccessArticle
Response Surface Methodology (RSM)-Based Evaluation of the 3D-Printed Recycled-PETG Tensile Strength
by
Lazaros Firtikiadis, Anastasios Tzotzis, Panagiotis Kyratsis and Nikolaos Efkolidis
Appl. Mech. 2024, 5(4), 924-937; https://doi.org/10.3390/applmech5040051 - 4 Dec 2024
Abstract
In this research, an investigation related to the tensile testing of 3D-printed specimens, under different fabrication parameters, is presented. The control samples were fabricated using Recycled-PETG: EVO (NEEMA3D™, Athens, Greece). It consists of recycled polyethylene terephthalate glycol (PETG) raw material, already used in
[...] Read more.
In this research, an investigation related to the tensile testing of 3D-printed specimens, under different fabrication parameters, is presented. The control samples were fabricated using Recycled-PETG: EVO (NEEMA3D™, Athens, Greece). It consists of recycled polyethylene terephthalate glycol (PETG) raw material, already used in industry, modified so that it becomes filament and can be printed again. More specifically, the parameters set to be studied are the percentage of infill, the speed and the type of infill. Both infill density and printing speed have three value levels, whereas for the infill pattern, two types were selected. Two sets of 18 specimens each were fabricated, with respect to the different parameter combinations. Through the results of the tests, the maximum tension of each specimen was obtained separately. Of the three parameters defined, it was found that the most important are the type of infill (44.77%) and the percentage of infill (24.67%). Speed (13.22%) did not strongly affect the strength of the specimens. In conclusion, the empirical model developed was considered reliable in terms of the value of the squared error, R-sq(pred) (97.72%), but also of the rest of the resulting analysis residual graphs (through the full factorial design).
Full article
(This article belongs to the Special Issue Early Career Scientists’ (ECS) Contributions to Applied Mechanics (2nd Edition))
►▼
Show Figures
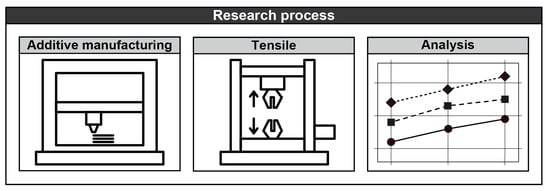
Figure 1
Open AccessArticle
Analysis of Damage Value of Aluminum Alloys—Application of a Continuum Damage Mechanics Model
by
Vishavbandhu Kanwar, Vishwanath Managuli and Y. S. Upadhyaya
Appl. Mech. 2024, 5(4), 908-923; https://doi.org/10.3390/applmech5040050 - 1 Dec 2024
Abstract
Damage refers to the degradation of a material subjected to an external condition such as loading, temperature, and environment. Several investigations have been undertaken to understand the damage of materials like steel, aluminum alloy, titanium alloy, and other materials. However, a comprehensive study
[...] Read more.
Damage refers to the degradation of a material subjected to an external condition such as loading, temperature, and environment. Several investigations have been undertaken to understand the damage of materials like steel, aluminum alloy, titanium alloy, and other materials. However, a comprehensive study on the range of damage values for various materials is scarce. Therefore, an attempt has been made in the current study to investigate the range of damage values of 32 aluminum alloys because of their widespread applications in the aerospace, railway, automotive, and marine industries. The damage value of materials is determined by incorporating the Continuum Damage Mechanics (CDM)-based Bhattacharya and Ellingwood model. This model demands the monotonic properties of materials as inputs, and these are obtained from the literature. The critical damage values of the alloys were determined, and their values vary in the range of 0.1 to 0.9. It was observed that damage value is primarily influenced by plastic strain. The variation in the damage value of aluminum alloys is also analyzed under different plastic strain conditions. The comprehensive results of critical damage value and the variation in the damage value of the aluminum alloys obtained helps in selecting an appropriate aluminum alloy for applications where damage criteria play a significant role.
Full article
(This article belongs to the Special Issue Early Career Scientists’ (ECS) Contributions to Applied Mechanics (2nd Edition))
►▼
Show Figures
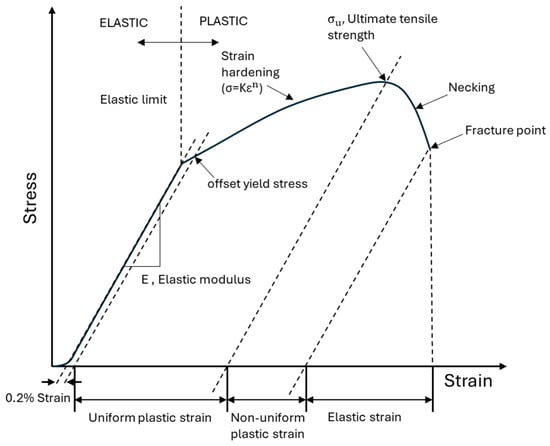
Figure 1
Open AccessArticle
In Silico Benchmarking of Fatigue Life Estimation Models for Passive SMD Solder Joints Under Thermal Cycling
by
Antal Bakonyi, Gusztáv Fekete and Ambrus Zelei
Appl. Mech. 2024, 5(4), 877-907; https://doi.org/10.3390/applmech5040049 - 25 Nov 2024
Abstract
Related to microelectronics’ reliability, lifetime estimation methods have gained importance, especially for surface-mounted devices. The virtual testing of electronic assemblies necessitates the geometry modeling and finite element analysis of the solder joint. The effect of the simplification of the solder geometry on the
[...] Read more.
Related to microelectronics’ reliability, lifetime estimation methods have gained importance, especially for surface-mounted devices. The virtual testing of electronic assemblies necessitates the geometry modeling and finite element analysis of the solder joint. The effect of the simplification of the solder geometry on the predicted lifetime is an open question. Furthermore, there is still not yet straightforward guidance for the choice of the material model and fatigue lifetime model. In this study, the impact of the geometry input method, the material model and the lifetime model choice is investigated on two different surface-mounted capacitors in a simulation-based benchmark analysis under thermal cyclic loading. Four different types of solder geometry modeling approaches are compared, among which one is a physics-based approach. Ten different fatigue models founded on plastic and viscoplastic material models are benchmarked. The results show that the component standoff height and the solder volume have a positive effect on the lifetime, while the capacitor size has a slightly negative effect on the lifetime. The results also suggest that approximate geometries can be used to replace the physics-based model with a restriction for the minimum standoff height.
Full article
(This article belongs to the Special Issue Early Career Scientists’ (ECS) Contributions to Applied Mechanics (2nd Edition))
►▼
Show Figures
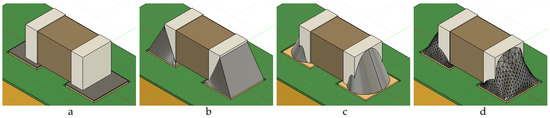
Figure 1
Open AccessArticle
Experimental Investigation of the Seismic Response of Small Freestanding Replicas of Ancient Vessels
by
Angeliki Papalou
Appl. Mech. 2024, 5(4), 856-876; https://doi.org/10.3390/applmech5040048 - 20 Nov 2024
Abstract
►▼
Show Figures
Monumental artifacts belong to our cultural heritage, and there is a great need to protect them from earthquake damage. This study experimentally investigates the behavior of replicas of ancient vessels under seismic excitations. Each vessel was placed on a wooden base, which was
[...] Read more.
Monumental artifacts belong to our cultural heritage, and there is a great need to protect them from earthquake damage. This study experimentally investigates the behavior of replicas of ancient vessels under seismic excitations. Each vessel was placed on a wooden base, which was attached to a shake table and was excited by earthquake signals. The effect of the amplitude of the excitation and the friction coefficient between the object and the base of support was examined. The dynamic response of the vessels included sliding and rocking, which, at high excitation levels, could involve rotation about their vertical axis and translation motion. High levels of excitation could cause the vessels to overturn but this did not always occur at the same level of excitation. The coefficient of friction is a key parameter of their behavior. If it is high, sliding motion is reduced while rocking parallel to the direction of excitation increases, starting at low excitation levels. This could lead to an early overturning of the object. The geometric characteristics and irregularities of the vessel can play an important role in its dynamic response.
Full article
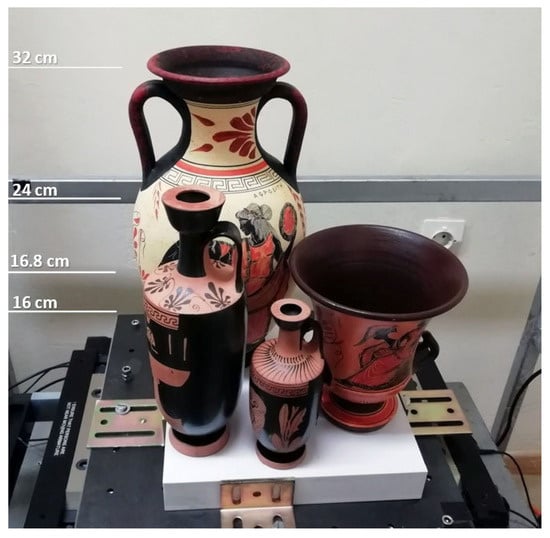
Figure 1
Open AccessArticle
Advanced Numerical Modeling and Experimental Analysis of Thermal Gradients in Gleeble Compression Configuration for 2017-T4 Aluminum Alloy
by
Olivier Pantalé, Yannis Muller and Yannick Balcaen
Appl. Mech. 2024, 5(4), 839-855; https://doi.org/10.3390/applmech5040047 - 13 Nov 2024
Abstract
►▼
Show Figures
Gleeble thermomechanical simulators are widely utilized tools for the investigation of high-temperature deformation behavior in materials. However, temperature gradients that develop within the specimen during Gleeble compression tests have the potential to result in non-uniform deformation, which may subsequently impact the accuracy of
[...] Read more.
Gleeble thermomechanical simulators are widely utilized tools for the investigation of high-temperature deformation behavior in materials. However, temperature gradients that develop within the specimen during Gleeble compression tests have the potential to result in non-uniform deformation, which may subsequently impact the accuracy of the measured mechanical properties. This study presents an experimental and numerical investigation of the temperature fields in 2017-T4 aluminum alloy specimens prior to Gleeble compression tests at temperatures ranging from utilizing uniform temperature distribution (ISO-T) tungsten carbide anvils. The use of multiple thermocouples, welded to both the specimen and anvils, offers valuable insights into the temperature gradients and their evolutions. A coupled thermal–electrical finite-element model was developed in Abaqus for the purpose of simulating the resistive heating process. A user amplitude subroutine (UAMP) is implemented to regulate the heating based on a proportional–integral–derivative (PID) algorithm that modulates the current density to follow the specified temperature profile. The numerical results demonstrate that the temperature gradients within the specimen at the end of the heating process, reaching a temperature of , are minimal, with values below . This is in accordance with the experimental observations. The addition of graphite foils between the specimen and anvils has been shown to effectively reduce the gradients. The use of the measured anvil temperature as a boundary condition, rather than a constant value of , has been demonstrated to improve the agreement between the simulated and experimental cooling curves. The modeling approach provides a framework for quantifying temperature gradients in Gleeble compression specimens and for assessing their impact on the measured constitutive response of materials at elevated temperatures.
Full article
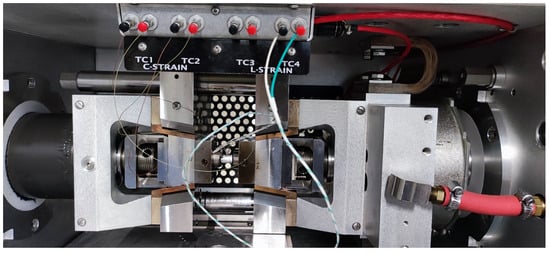
Figure 1
Open AccessArticle
Improvement of Stockbridge Damper Design for Cable-Stayed Bridges
by
Adél Olosz, Balázs Kövesdi, Péter Hegyi and László Dunai
Appl. Mech. 2024, 5(4), 818-838; https://doi.org/10.3390/applmech5040046 - 12 Nov 2024
Abstract
Stockbridge dampers are widely used to mitigate the vibrations of cable-stayed bridges and of many other cable-suspended or cable structures exposed to the action of pedestrians, traffic or wind load. Within the current research work, one of the most effective and likely used
[...] Read more.
Stockbridge dampers are widely used to mitigate the vibrations of cable-stayed bridges and of many other cable-suspended or cable structures exposed to the action of pedestrians, traffic or wind load. Within the current research work, one of the most effective and likely used damper types, the Stockbridge damper, was investigated to support its design and application within the daily engineering praxis. The Stockbridge damper has a relatively simple structural layout, which ensures its modular design allows it to easily adapt the damper to cables having different dynamic properties (eigenfrequencies, mass, etc.). This paper focuses on two main research areas: (i) to understand the static and dynamic behaviour of the damper and the stay cable interaction to investigate the effectiveness of its damping; (ii) to study the sensitivity of the natural frequencies of the damper to the design parameters. The final aim of the research is to develop a simple design method that is easy to apply in engineering practice and allows the efficient adaptation of the Stockbridge damper to different cable-stayed bridges. Key findings include the recommendation to position the damper at approximately 20% of the cable length for optimal attenuation, the importance of detuning to maintain effectiveness under varying cable forces, and the observation that increasing the damper mass improves efficiency, particularly for detuned elements.
Full article
(This article belongs to the Special Issue Mechanical Design Technologies for Beam, Plate and Shell Structures (3rd Edition))
►▼
Show Figures
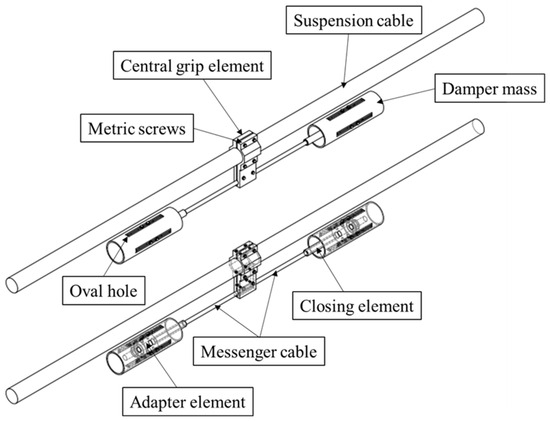
Figure 1
Highly Accessed Articles
Latest Books
E-Mail Alert
News
Topics
Topic in
Applied Mechanics, Applied Sciences, Materials, Polymers, Solids, Metals
Multi-scale Modeling and Optimisation of Materials
Topic Editors: Mustafa Awd, Frank WaltherDeadline: 31 July 2025
Topic in
Applied Mechanics, Energies, Processes, Sustainability, Wind
Wind Energy in Multi Energy Systems
Topic Editors: Zhe Chen, Davide Astolfi, Tingting ZhuDeadline: 31 December 2025
Topic in
Applied Mechanics, Applied Sciences, Buildings, CivilEng, Infrastructures
Advances on Structural Engineering, 3rd Edition
Topic Editors: Jong Wan Hu, Junwon SeoDeadline: 31 March 2026

Conferences
Special Issues
Special Issue in
Applied Mechanics
Mechanical Design Technologies for Beam, Plate and Shell Structures (3rd Edition)
Guest Editor: César VasquesDeadline: 28 February 2025
Special Issue in
Applied Mechanics
Vibration Monitoring of Wind Turbines: Predicting the Remaining Useful Life
Guest Editor: Juan Carlos JaureguiDeadline: 30 June 2025
Special Issue in
Applied Mechanics
Thermal Mechanisms in Solids and Interfaces
Guest Editor: Jude OsaraDeadline: 31 July 2025
Topical Collections
Topical Collection in
Applied Mechanics
Fracture, Fatigue, and Wear
Collection Editor: Magd Abdel Wahab